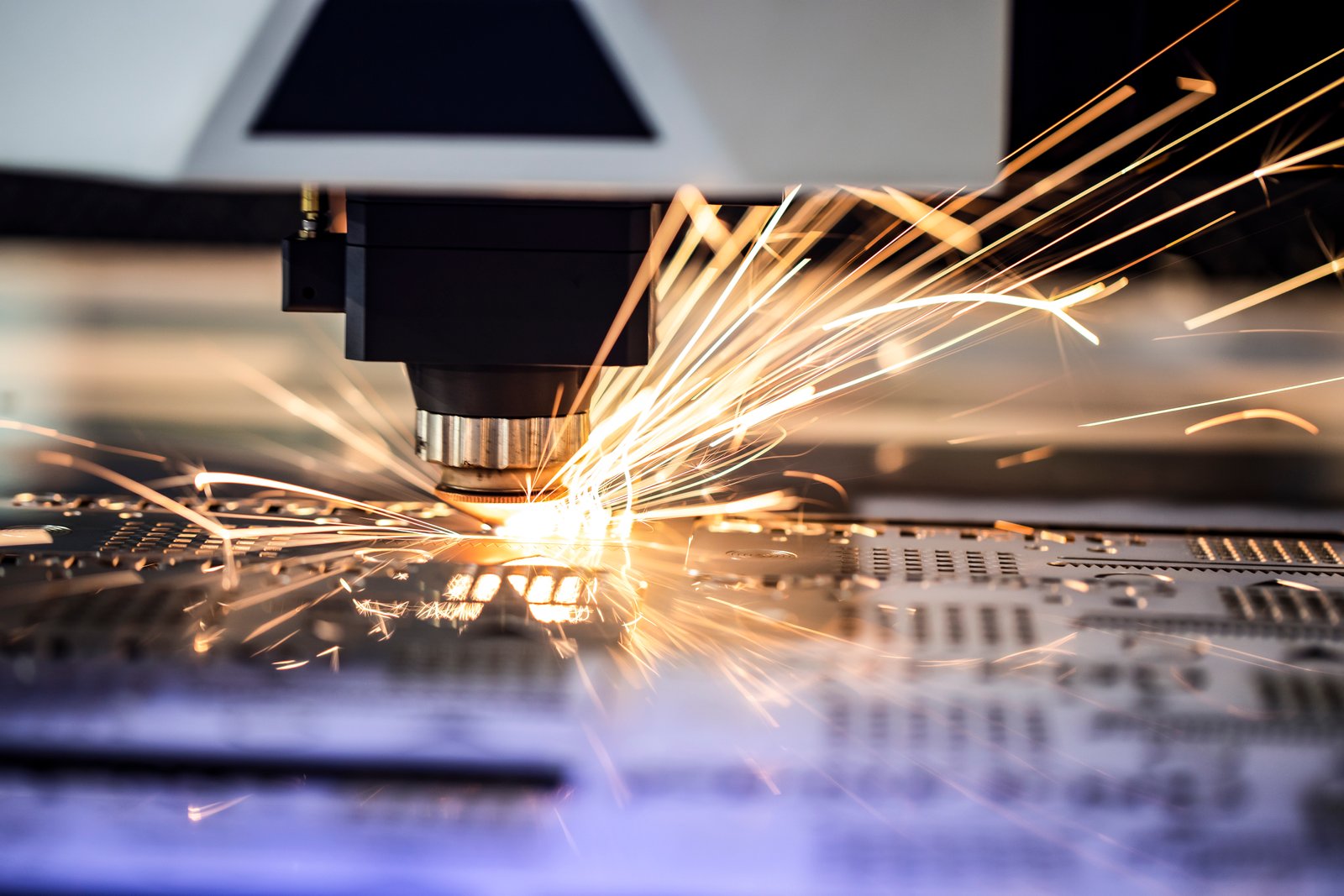
Cutting metal is a crucial process in many industries, and choosing the right cutting method can significantly impact the efficiency and quality of the final product. At Century Steel, a stainless steel and aluminum trader and steel fabricator in Kuwait. One of our most advanced offerings is fiber laser cutting. In this blog, we'll compare fiber laser cutting with other common cutting methods, highlighting their advantages and disadvantages to help you make an informed decision for your projects.
What is Fiber Laser Cutting?
Fiber laser cutting is a cutting-edge technology that uses a high-powered laser beam to cut materials with precision and speed. This method is known for its accuracy, efficiency, and ability to cut complex shapes with minimal waste.
Learn more about Fiber Laser Cutting
Comparing Cutting Methods
Plasma Cutting
Plasma cutting uses a high-velocity jet of ionized gas (plasma) to cut through electrically conductive materials. It is commonly used for cutting steel, stainless steel, and aluminum.
Advantages of Plasma Cutting:
- Speed: Plasma cutting is faster than many traditional methods, especially for thicker materials.
- Cost: Generally, plasma cutting equipment is less expensive than fiber laser cutting machines.
- Versatility: Effective for cutting thick metals and can handle materials up to several inches thick.
Disadvantages of Plasma Cutting:
- Precision: Not as precise as fiber laser cutting, which can lead to rougher edges.
- Heat: Generates a lot of heat, which can distort materials and affect cut quality.
Water Jet Cutting
Water jet cutting uses a high-pressure stream of water, sometimes mixed with abrasive materials, to cut through a wide variety of materials, including metals, glass, ceramics, and composites.
Advantages of Water Jet Cutting:
- No Heat: It is a cold cutting process, so there's no heat-affected zone (HAZ), which prevents material distortion.
- Versatility: Can cut through virtually any material, from soft rubber to hard metals.
- Precision: Produces very precise cuts with smooth edges.
Disadvantages of Water Jet Cutting:
- Speed: Slower than fiber laser and plasma cutting, especially for thicker materials.
- Cost: Can be expensive due to the need for abrasives and high maintenance.
Oxy-Fuel Cutting
Oxy-fuel cutting involves using a torch to heat metal to its ignition temperature and then cutting it with a stream of oxygen. It is mainly used for cutting thick steel plates.
Advantages of Oxy-Fuel Cutting:
- Thickness: Can cut through very thick materials, up to several inches of steel.
- Portability: Equipment is relatively simple and can be used in various locations.
Disadvantages of Oxy-Fuel Cutting:
- Precision: Not as precise as fiber laser or water jet cutting.
- Heat: Generates a significant amount of heat, which can lead to material distortion and a larger heat-affected zone (HAZ).
Mechanical Cutting
Mechanical cutting methods include processes like sawing, milling, and drilling. These methods physically remove material using tools with cutting edges.
Advantages of Mechanical Cutting:
- Cost: Generally, mechanical cutting tools are less expensive than advanced cutting machines.
- Availability: Tools are widely available and can be used for various materials.
Disadvantages of Mechanical Cutting:
- Precision: Not as precise as fiber laser or water jet cutting.
- Wear and Tear: Tools can wear out quickly, requiring frequent maintenance and replacement.
Electric Discharge Machining (EDM)
EDM uses electrical discharges (sparks) to cut materials. It is mainly used for cutting hard metals and intricate shapes.
Advantages of EDM:
- Precision: Extremely precise, capable of cutting complex shapes with fine details.
- No Contact: No physical contact with the material, reducing mechanical stress and distortion.
Disadvantages of EDM:
- Speed: Relatively slow compared to other cutting methods.
- Cost: Equipment can be expensive, and the process consumes a lot of electrical energy.
Comparison Table
Cutting Method |
Precision |
Speed |
Cost |
Material Thickness |
Heat Generation |
Versatility |
Fiber Laser Cutting |
High |
Very Fast |
High |
Thin to Medium |
Low |
High |
Plasma Cutting |
Medium |
Fast |
Medium |
Thick |
High |
Medium |
Water Jet Cutting |
High |
Slow |
High |
Thin to Thick |
None |
Very High |
Oxy-Fuel Cutting |
Low |
Medium |
Low |
Very Thick |
Very High |
Low |
Mechanical Cutting |
Medium |
Medium |
Low |
Thin to Medium |
Medium |
Medium |
EDM |
Very High |
Slow |
High |
Thin to Medium |
None |
Medium |
Why Choose Fiber Laser Cutting?
After comparing these methods, it’s clear that fiber laser cutting offers several significant advantages:
- Precision and Quality: Provides superior precision, allowing for detailed and complex cuts with minimal waste.
- Speed: Faster cutting speeds make it ideal for high-volume production.
- Versatility: Suitable for various materials and thicknesses, providing flexibility in different applications.
- Efficiency: Minimal heat-affected zone reduces the risk of warping or altering material properties, ensuring a high-quality finish.
Conclusion
Each cutting method has its unique strengths and weaknesses. Fiber laser cutting stands out for its precision, speed, and quality, making it ideal for detailed and high-volume work. However, other methods like plasma cutting, water jet cutting, oxy-fuel cutting, mechanical cutting, and EDM offer their own advantages depending on the material and specific requirements of the job. Understanding these differences can help you choose the best cutting method for your needs.
We offer high-quality, precise and efficient fiber laser cutting service in Kuwait at Century Steel. We use top-notch equipment and have a skilled team to offer you excellent results for various materials. Contact us today for further inquiries.